Maximizing Electrical Safety with the Right Electrical Insulation Tape
Electrical insulation tape is a critical component that safeguards and insulates various kinds of electrical wires and cables. This essential material, often called insulating tape, is vital for maintaining safety standards in both commercial and residential settings. By effectively averting electrical shorts and safeguarding against moisture, dust, and abrasion, this tape ensures that electrical systems remain functional and reliable. Acknowledging the importance of this tool can help you prevent potential hazards and create a well-organized workspace, significantly enhancing overall safety and efficiency.
Available in an array of sizes, lengths, and colors, electrical insulation tape is tailored for various applications. These diverse options not only enhance insulation effectiveness but also facilitate the identification and organization of cables through color-coding. By employing different colors, you can streamline your electrical tasks for quick identification of specific wires, which greatly enhances productivity and organization during electrical projects. This thoughtful approach can significantly reduce errors and improve workflow efficiency.
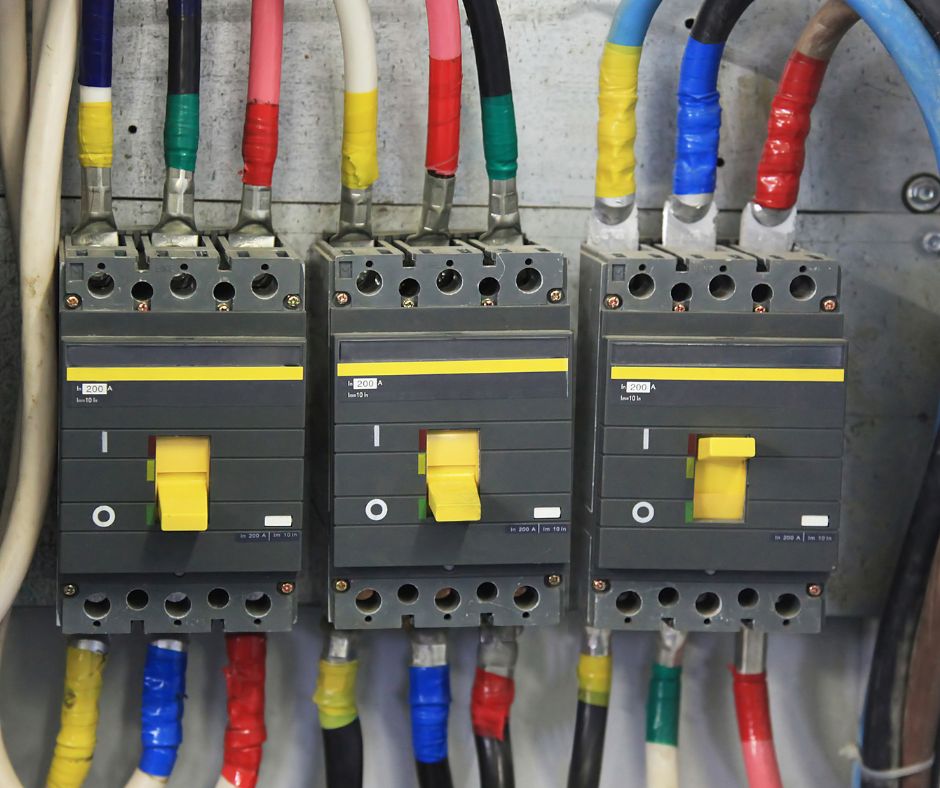
Recognizing the Critical Conditions Under Which Electrical Tape Melts
Indeed, electrical tape can melt under specific conditions that require careful monitoring. This discussion will thoroughly examine the temperature thresholds relevant to electrical tape, detail the circumstances that may lead to melting, and highlight critical signs of overheating that necessitate vigilant observation. Understanding these factors is crucial for ensuring the safe and effective use of electrical insulation tape across a range of applications, thereby enhancing safety and reliability.
Navigating the Temperature Limits of Electrical Tape for Optimal Safety
Like many materials, electrical tape has established temperature limits that are essential for its safe usage. Most standard types can tolerate temperatures up to approximately 80°C, while some heavy-duty variants are specifically designed to endure slightly higher temperatures. When subjected to conditions that surpass these thresholds, the integrity of the tape may begin to degrade, resulting in potential failures that can compromise safety and functionality. It's imperative to be aware of these limits to prevent unforeseen issues.
As temperatures rise and approach the maximum threshold, the performance of electrical tape can begin to deteriorate. This degradation may manifest in various forms, including melting, a sticky or gooey texture, or, in severe cases, complete failure of the tape. Being aware of these temperature limitations is vital for maintaining safety in electrical applications, ensuring that your projects proceed without unnecessary risks or complications that could lead to hazardous situations.
For environments exposed to extreme temperatures, it is advisable to opt for high-temperature variants of electrical tape. For example, heat-resistant tape, made from materials such as fiberglass or silicone, can withstand temperatures of up to 200°C or even higher, making it an excellent choice for applications subjected to significant heat, ensuring both durability and safety.
Also Read: Keep Your Pets Safe Around Electricity
Request Your Quote Today!
Learn About Our FREE Electrical Inspections
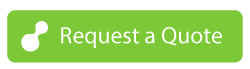
Identifying the Primary Factors Contributing to the Melting of Electrical Tape
Electrical tape may melt due to various underlying factors, primarily caused by exposure to excessive heat. Understanding these causes is vital for ensuring safe and efficient usage. Here are some of the most common reasons that contribute to the melting of electrical tape:
Exploring the Consequences of Overexposure to Heat on Electrical Tape
The primary cause of electrical tape melting is its proximity to high temperatures. If the tape is positioned near hot surfaces, engines, or any components generating heat, it may begin to soften, bubble, or even completely melt. Furthermore, electrical systems such as power circuits can produce heat levels that exceed the tape's rated capacity, particularly during operational malfunctions or overload scenarios, leading to potential hazards.
Thus, when utilizing electrical tape in areas prone to high temperatures, it is essential to verify the temperature ratings of the tape. This precaution helps prevent potential failures and ensures safety during application, safeguarding both equipment and personnel.
Investigating How Environmental Degradation Impacts Electrical Tape Performance
Electrical tape is not designed for eternal durability. Over time, both the adhesive and the tape material can degrade, especially when exposed to ultraviolet (UV) light, moisture, or other harsh environmental conditions. Such degradation can significantly reduce the insulating capabilities of the tape. As the tape ages, it may become less effective, exhibiting increased susceptibility to melting even at temperatures that would typically be manageable.
Routine wear and tear are expected in the lifecycle of electrical tape. Therefore, conducting regular inspections for any signs of aging or damage is essential to ensure continued safety and effective performance in electrical applications.
Understanding the Risks of Improper Application of Electrical Tape
Applying electrical tape under inappropriate conditions can lead to its premature failure. For instance, if the tape is wrapped too tightly, exposed to friction or elevated temperatures, or overstretched during application, its overall performance may be compromised. Additionally, wrapping the tape around sharp edges or applying it to components prone to overheating, such as light bulbs or electrical outlets, can pose problems unless the tape is specifically rated for those applications.
Also Read: 10 Ways to Save On Power And Energy Costs
Recognizing Key Signs That Indicate Electrical Tape is Overheating
If you suspect that your electrical tape is overheating, it is essential to monitor several key indicators closely. Here are the most common signs that may suggest your tape is melting or experiencing excessive heat:
Detecting a Sticky or Tacky Texture in Overheated Electrical Tape
A noticeable change in texture, especially a sticky or tacky feel, is often one of the first signs of melting electrical tape. This alteration can act as an early warning signal of further degradation, indicating that the tape may no longer provide adequate insulation, thereby posing a safety risk.
Identifying Discoloration as a Critical Sign of Heat Damage
Overheated electrical tape may exhibit significant discoloration. You might observe a shift from its standard black or colored appearance to shades of brown, dark gray, or even black. This change occurs as heat decomposes the tape's PVC or other materials. Early detection of this issue can prevent further damage to your wires and reduce the risk of electrical fires. If left unaddressed, it may lead to melting or create serious fire hazards, making vigilance paramount.
Observing Bubbling or Distortion as Indicators of Excessive Heat
If electrical tape begins to bubble, distort, or warp, it indicates that heat is adversely affecting its structure. This typically occurs when heat causes the adhesive or plastic layers to separate or degrade. The surface may appear wavy or uneven, signaling that temperatures exceed safe levels. Upon observing these bubbles, it is advisable to consult your electrician for a thorough evaluation of the situation to prevent further complications.
Identifying a Burning Smell as a Serious Warning
A burning smell near electrical tape is a critical warning sign that should never be overlooked. This odor may resemble melting plastic or burning rubber. When excessive heat causes the adhesive to break down, the resulting fumes can be alarming and hazardous. Do not dismiss this warning. If you detect a burning smell, it may indicate that the tape is on the verge of melting or potentially catching fire, necessitating immediate action.
Visible Smoke as a Major Indicator of Danger
If you notice smoke emanating from the electrical tape, it is a clear indication that the heat levels have far exceeded the tape's capacity. Smoke is a strong signal that the tape has likely started to melt or may even be igniting. At this critical juncture, it is vital to turn off the power source immediately and seek assistance from your electrician to ensure safety.
Remember – Never use water to extinguish an electrical fire. Instead, use a CO2 fire extinguisher for safety and effective action.
Essential Safety Steps to Follow If Electrical Tape Melts
If your electrical tape melts, the first step is to disconnect any power sources or switch off any equipment to ensure safety.
Prioritizing safety is crucial, as electrical hazards can pose significant risks to both life and property. Taking immediate action is vital to mitigate further danger.
Once you have ensured that the area is safe, always consult your electrician for professional guidance. If a professional installed the tape, they may need to inspect the area for any underlying electrical issues that could have contributed to the problem, ensuring a comprehensive approach to safety and functionality in your electrical systems.
Exploring Effective Alternatives to Electrical Tape for High-Temperature Settings
If you frequently work in environments where temperatures exceed the limits of standard electrical tape, consulting your electrician about suitable alternatives is wise. Here are several options that are worth considering:
- Heat-resistant silicone tape: This specialized tape is designed to withstand elevated temperatures and is perfect for applications where heat poses a significant risk.
- Fiberglass tape: A robust alternative that can handle extreme temperatures without compromising performance or safety, making it a reliable choice.
- Mica or ceramic insulation: For the highest level of heat protection, specialized insulations such as mica or ceramic are excellent choices, providing superior safety in high-temperature environments.
Understanding the Dangers Associated with Melting Electrical Tape
In summary, electrical tape can indeed melt, primarily due to exposure to excessive heat. Understanding the temperature limits of your tape and ensuring you select the appropriate type for your specific application are critical steps in preventing potential issues that could lead to serious consequences.
By staying alert to signs such as discoloration, stickiness, or unusual smells, you can take swift action to mitigate risks associated with electrical systems. Always prioritize safety and do not hesitate to reach out to your local electrician for expert advice when needed, ensuring your environment remains safe and functional.
Request Your Quote Today!
Learn About Our FREE Electrical Inspections
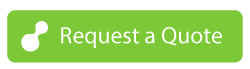
The Article: Does Electrical Tape Melt? Here’s What You Need to Know first appeared on https://writebuff.com
The Article Electrical Tape Melting: Essential Facts You Should Know Was Found On https://limitsofstrategy.com
The Article Electrical Tape Melting: Key Facts You Need to Know First Appeared ON
: https://ad4sc.com
Comments are closed